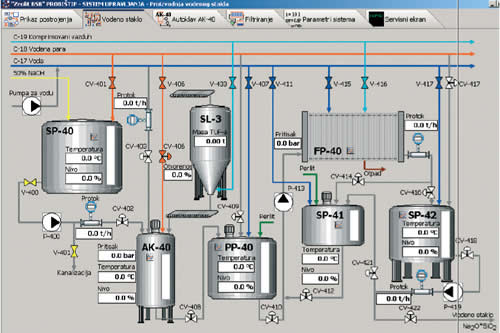
11 Oct Proizvodnja vodenog stakla i Foundation Fieldbus tehnologija
Uvod: Učiti na primeru
Načevši temu Foundation Fieldbus (FF) tehnologije u prošlom broju, nije mi bila ideja da ostanemo na temeljima teoretskih postavki ove relativno nove tehnologije u gazdovanju procesnim postrojenjima. Naprotiv, namera je da čitaocu, u prvom koraku, pomognemo da problem realizacije sistema nadzora i upravljanja jednim tehnološkim procesom sagleda iz drugog ugla, iz perspektive koju otvara Foundation Fieldbus. Doista, jednim člankom nije moguće sasvim razotkriti, ni dovoljno duboko zagrebati u materiju koja ima višedimenzionalnu i široku osnovu.
Pokušajmo da do novih spoznaja i zaključaka dođemo razmatrajući realizaciju konkretnog zadatka. U tu svrhu će nam poslužiti primer izvođenja Sistema za nadzor i upravljanje proizvodnjom vodenog stakla u čijoj realizaciji sam učestvovao kao koordinator tima. Reč je o fabrici (u izgradnji) za proizvodnju zeolita u Probištipu – Makedonija. Proizvodnja vodenog stakla je prva faza i zaokružena tehnološka celina u sastavu ovog objekta.
Opis: Proizvodnja vodenog stakla
Proizvodnja vodenog stakla podrazumeva sledeće medije:
- Finalni proizvod:
- Na2O* SiO2 – vodeno staklo (tečni natrijum silikat)
- Sirovine:
- Tuf – amorfni silicijum dioksid (granulat)
- NaOH 50% – pedesetoprocentni natrijum hidroksid
- H2O – voda
- Pomoćni mediji:
- Suvozasićena vodena para – T= 180 oC
- Komprimovani vazduh – T= Tamb. ; p= 6 bar
Tehnološki postupak
Tehnološka šema postrojenja za proizvodnju vodenog stakla data je na Slici br.1 kroz izgled jednog ekrana sa PCoperatorske radne stanice.
Rastvor (50%) natrijum hidroksida se doprema autocisternama i skladišti u sud SP-40. Predviđeno je kontinualno merenje temperature (TT 401) i nivoa (LT 401) u SP-40. Temperatura u ovom sudu se automatski održava iznad -5 oC puštanjem vodene pare kroz cevni izmenjivač toplote.
TUF se u granulama 1 do 3 mm dovozi i skladišti u bunker TUF-a. Ovaj materijal se transportnim sistemom (transportne trake i elevatori) doprema u vagu SL-3 i iz nje otprema u reakcioni sud AK-4. Proces odmeravanja željene količine TUF-a, što podrazumeva zadavanje mase, njeno kontinualno merenje, te punjenje i pražnjenje vage kontroliše Upravljački sistem.
Ovaj, inače šaržni proces podrazumeva automatsko, maseno odmeravanje i druge dve komponente koje učestvuju u reakciji (voda i lužina). Tečni mediji se odmeravaju preko elektromagnetnih merača protoka i On- Off ventila.
Reakcija se odvija na 180 oC i pritisku od 5 bar. Rezultat reakcije u prvom delu procesa je nefiltrirano vodeno staklo koje se smešta u rezervoar PP- 40. U autoklavu AK-40 se vrši regulacija temperature reakcije i meri pritisak. Drugi deo procesa je filtriranje kroz filter-presu FP-40 koja ima sopstvenu upravljačku jedinicu (PLC). Vodeća veličina za proces filtriranja je pritisak medija na ulazu u FP-40. Filtrirano vodeno staklo se skladišti u posudi SP-42. Posuda SP-41 služi za pripremu rastvora prvog nanosa. U svim posudama se mere nivoi tj mase medija koji su u njima kao i temperatura. Na izlazu iz filter-prese i suda SP-42 meri se protok vodenog stakla.
Nadzor i upravljanje: Arhitektura sistema
Arhitektura čitavog sistema je postavljena na bazi Foundation Fieldbus (FF) tehnologije. Mernoregulaciona oprema u pogonu, uređaji za vezu, mrežne komponente, radne stanice, komunikacije kao i softver za konfigurisanje sistema i izradu aplikacije izabran je u skladu sa ovim standardom. Posmatrajući postavljenu arhitekturu vidimo da se sistem sastoji od mreže FF uređaja u polju koji su međusobno povezani na dve čisto digitalne i dvosmerno-komunikacione grane (FF H1). One preko univerzalnog mosta izlaze na viši komunikacijski nivo – industrijsku ethernet mrežu velike brzine (HSE). Ovo su jedina dva vertikalno povezana komunikaciona nivoa koje definiše Foundation Fieldbus. Postojeći analogni ulazno-izlazni (U/I) signali su preko analognih kartica i istog mosta vezani za ostatak sistema.
Diskretni U/I signali hardverski gravitiraju, preko DI i DO kartica, drugom delu sistema za koji je zadužen modul sa logičkim koprocesorom (PLC). Komunikaciono je ova celina, preko gateway kartice i iste ethernet mreže, koristeći standard Modbus TCP/ IP, povezana sa »kontinualnim« delom sistema. Svi postojeći podaci iz procesnog dela sistema su dostupni softverskim aplikacijama na radnim stanicama zahvaljujući OPC standardu. Aplikativni software za nadzor i upravljanje postrojenjem je izrađen korišćenjem tri sistemska softverska alata.
- Prvi je jedinstveni program za konfiguraciju sistema i rešavanje upravljačkih strategija u FF okruženju (Syscon).
- Drugi je zadužen za izvršenje diskretne upravljačke logike (interlocking) pisanjem ladder dijagrama (LogicView).
- Treći je alat za izradu HMI aplikacije na radnim stanicama (Delphi).
Pomeranje granica
Koje ciljeve i zahteve je Upravljački sistem morao da ispuni?
1.Sistem mora da bude decentralizovan i nadogradiv. Izvesti punu automatizaciju dela fabrike (vodeno staklo) pre nego što je i izgrađen ostatak pogona (zeolit).
2.Omogućiti jednostavnu promenu procesnih parametara. Tri su razloga za postavljanje ovog zahteva. Jedan je taj što se radi o novom tehnološkom postupku pa je potrebno pronaći njegove optimalne parametre u probnom radu. Drugi je promenljivost kvaliteta ulaznih sirovina i treći namera projektanta da isti pogon, na osnovu zahteva tržišta, proizvodi više različitih proizvoda.
3.Minimizirati cenu i vreme završetka prve faze. Želja investitora je bila da što pre tržištu ponudi proizvod (vodeno staklo) i postane kreditno sposoban, što bi dalo finansijski zamajac završetku cele fabrike.
- Integrisati opremu, paket jedinice, koje imaju sopstveno upravljanje (Filter presa).
- Preduprediti neželjene zastoje i krajnje pojednostaviti održavanje postrojenja tj minimizirati troškove u radu.
- Obezbediti pouzdan i bezbedan rad postrojenja.
- Omoguiti kasniju integraciju u budući informacioni sistem preduzeća.
Da bih bio potpuno jasan, moram da naglasim da usvajanje, makar i najboljih alata za obavljanje nekog posla ne garantuje njegovo uspešno izvršenje. Kad je zadatak optimizacija rada tehnološkog procesa, koji se najčešće zanemari kada postrojenje proradi, ova konstatacija je apsolutno tačna. Dakle, da bi jedno procesno postrojenje radilo sa maksimalnim profitom mora da ga uspostave i prate ljudi, stručnjaci, dobri poznavaoci postavljene tehnologije, tehnike procesnih merenja i automatskog upravljanja.
Na koji način, i koliko uspešno je primena FF tehnologije mogla da pomogne rešavanju postavljenih zadataka? 1.Uvođenjem „inteligentnih“, mikroprocesorskih uređaja u polju i njihovim povezivanjem u fieldbus mrežu dobio se potpuno distribuiran upravljački sistem i izbrisana je granica između centralne-upravljačke i perifernemernoregulacione opreme. Zbog toga što ne postoji izrazita centralna jedinica, dodavanje svakog novog uređaja u polju predstavlja jačanje celog sistema. Kod klasičnih upravljačkih sistema novi merni uređaj znači dodatno opterećenje za centralni procesor.
Dakle, FF nam je omogućio da postavimo optimalnu arhitekturu dela sistema vezanog za vodeno staklo ne vodeći računa kako će on izgledati na kraju za celu fabriku. Moguće je dodavanje novih uređaja u polju i „na živo“, bez isključenja napajanja za FFH1 grane. Budući delovi sistema će biti samo novi nodovi na ethernet (HSE) mreži. 2.Pošto se radi o šaržnom postupku, gde je za kvalitet proizvoda jako bitan odnos količina usutih komponenti u reaktor, te temperatura i pritisak na kome se reakcija odvija, omogućeno je glavnom tehnologu da menja odnose komponenti (recepturu) i zadaje procesne parametre. Sa svakog FF uređaja u pogonu imamo čitav skup različitih procesnih i dijagnostičkih informacija, koje možemo učiniti dostupnim operateru, tehnologu, službi održavanja ili menadžmentu fabrike. Zahvaljujući FF tehnologiji, regulaciono kolo po temperaturi je realizovano lokalno, između transmitera temperature i pozicionera. Ulogu regulatora je preuzeo procesor pozicionera na regulacionom ventilu izvršavajući upravljački algoritam kroz PID funkcionalni blok. Promena parametara P, I, D ovog regulatora su dostupni operateru. Odmeravanje zadatih tečnih komponenti i ulogu „batch“ kontrolera preuzeli su merači protoka vode, odnosno lužine. Znajući gustinu lužine uzorkovanjem i unoseći njenu vrednost u aplikaciju dobili smo mogućnost masenog odmeravanja svih komponenti. 3.Vreme realizacije ovakvog projekta je prepolovljeno zahvaljujući primeni Foundation Fieldbus tehnologije gotovo u svim domenima. Imajući u vidu nejasne granice projektnog zadatka zbog do kraja nedefinisane tehnologije rada postrojenja, koristeći jednostavnost i prilagodljivost arhitekture Sistema, projektna dokumentacija je mogla da bude urađena znatno brže i da trpi kasnije česte izmene do konačne verzije projekta izvedenog stanja. Multidrop arhitektura (povezivanje većeg broja uređaja na jednu paricu) omogućila je višestruku uštedu u kablovima i količini opreme u ormanu automatike. Kabliranje u pogonu i ožičenje ormana je urađeno brže, jednostavnije tj jeftinije. Softverska konfiguracija i parametriranje komponenti FF sistema je urađena van pogona čim je oprema stigla i njeno „oživljavanje“ u procesnim uslovima se svelo na fizičko povezivanje i stavljanje po napon.
4.Opredeljujući se za Foundation Fieldbus investitor se nije opredelio za isključivog isporučioca opreme od koga će zavisiti u budućnosti. U našem slučaju integrisana je oprema koja odgovara FF-standardu dva proizvođača (Smar i Krohne). S druge strane specifični delovi procesne opreme koje se isporučuju sa svojim upravljačkim jedinicama se jednostavno integrišu u ovaj otvoreni sistem. PLC filter-prese proizvođača Netzsch integrisan je na nivou diskretnih signala.
5.Zapravo najveća korist od primene FF tehnologije je njena eksploatacija u radu postrojenja. Ona povećava raspoloživost pogona tj minimizira i eliminiše neželjene zastoje ili havarije, koje mogu svojim troškom da višestruko prevaziđu vrdnost investicije u automatizaciju. Na koji način? U filozofiju FF-a je ugrađena dijagnostika o kvalitetu rada postrojenja u četiri nivoa.
- Kvalitet varijable – Na primer, vrednost pritiska sa transmitera pritiska uvek prati i informacija o kvalitetu tog podatka (dobar, loš ili nesiguran).
- Kvalitet rada mernog instrumenta – Isti transmiter pritiska će nam „javiti“ da je merna ćelija oštećena ili neki deo elektronike ne obavlja svoju funkciju.
- Kvalitet rada regulacione petlje – Pozicioner koji, pored svoje osnovne funkcije izvršava zadatak regulacije, na primer pritiska, može da signalizira neregularan rad ili prekid petlje i da preuzme brigu o regulacionom ventilu (potpuno ga zatvori, otvori ili zadrži zatečeno stanje).
- Kvalitet rada okolne procesne opreme, dela ili celog postrojenja – Zahvaljujući obilju korisnih informacija, moguće je uz dobro poznavanje fizikalnosti tehnološkog procesa, vrlo precizno dijagnosticirati ne samo stanje nego pogoršanje kvaliteta rada procesne opreme. Na primer, analizom signala o pritisku na instalaciji u vremenu može se uočiti kavitacija ili habanje ležajeva na obližnjoj centrifugalnoj pumpi i planirati njen remont. Neočekivana promena protoka u cevovodu može značiti kristalizaciju medija u njemu te se može reagovati pre njegovog zapušenja i neplaniranog zastoja.
Na osnovu svega iznetog može se lako zaključiti da je održavanje ovakvog procesa svedeno na intervenciju u planirano vreme zaustavljeanja postrojenja, sa unapred poznatim radnim zadatkom. Deluje se samo na određene delove opreme, sa unapred pripremljenim rezervnim delovima i alatom.
6.Višeslojnom dijagnostikom rada, ukrštanjem informacija iz procesa sa različitih FF-uređaja postignuta je visoka pouzdanost njegovog obavljanja i obezbeđena visoka bezbednost rada po ljude i opremu. Zaštita procesa i sistema od neovlašćenih pristupa se vrši uvođenjem korisničkih imena i šifara. Svaki korisnik se prijavljuje a u bazi sistema se nalazi i njegov nivo pristupa. Tako na primer prelazak na servisni režim i daljinsko komandovanje može všiti samo radnik održavanja dok parametre mogu menjati samo inženjeri održavanja i tehnolozi.
7.Činjenica da je ethernet (HSE) već deo komunikacione arhitektuire ugrađen u Foundation Fieldbus standard ga čini potpuno ovorenim i zapravo začetkom buduće lokalne računarske mreže preduzeća. Izveštaji koje danas direktor fabrike i menadžeri prodaje, nabavke i marketinga dobijaju u štampanoj formi sa printera u kontrolnoj sobi će tada dospevati u elektronskoj formi mrežom na lični PC.
Zaključak: Samo prvenac
Opisani primer predstavlja samo jedan od početnih i skromnih doprinosa naših stručnjaka na usvajanju i praktičnoj primeni Foundation Fieldbus tehnologije na balkanskim prostorima. I sam svestan da prodiranju novina u načinu razmišljnja i pristupu rešavanju tehničkih problema mora da prethodi edukacija za koju je je potrebno vreme i puno entuzijastičkog rada, ne mogu da budem nezadovoljan tempom prodora Foundation Fieldbus tehnologije na naše prostore. Postoji, kod nas, grupa od desetak kvalitetnih inženjera iz oblasti upravljanja tehnološkim procesima koji se trude da u svojim radnim okruženjima, kroz praktične primere pokažu svojim korisnicima, kolegama ili rukovodiocima prednosti i korist koju može da donese FF.